What is a Relay ?
Relays are electronic switches used when an independent low-voltage signal is needed to control a high-power circuit. They commonly use an electromagnet (coil) to operate their internal mechanical switching mechanism (contacts). The relay coil that produces the magnetic field may only consume fractions of a watt of power, while the contacts closed or opened by that magnetic field may carry hundreds of times that amount of energy to a load.
The most popular type of relay is an Electromechanical relay. Other types of relay have similar functionalities with different switching mechanisms.
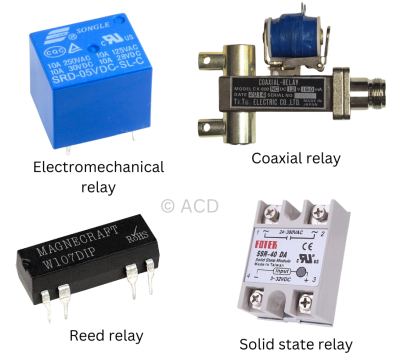
Use of relay
The primary purpose of a relay is to control a high-voltage circuit using a low-voltage control signal. It galvanically isolates the low voltage from the high voltage, protecting the sensitive low voltage components.
Working principle of relay
The working principle of a relay is simple. When a voltage is applied to the electromagnetic coil, a current builds up through the coil. This current magnetizes the iron core and generates a magnetic field, attracting the armature connected using a spring. Depending on the construction, the relay closes or opens the load circuit. When the voltage is removed, the armature and spring returns to its idle position.
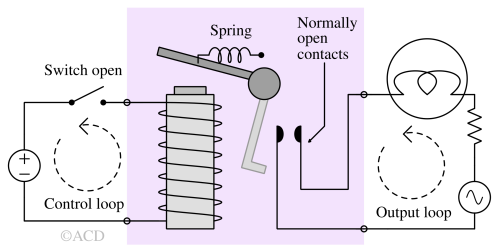
Here’s an example of a normally open (NO) relay circuit. The control switch (on the left) is open, meaning the coil is not energized. The spring is in idle position, and the contacts are open. The high voltage/current lamp is turned off. In the second figure, the coil is energized as soon as the control switch is turned on, creating a magnetic field. The magnetic field attracts the metal armature. The spring is extended. The contacts touch each other and close the lamp circuit. This results in turning on the lamp. Please note that the current on the control side (left side) could be carrying only micro to milli ampere, but the controlled side (right side) can carry in amperes (A).
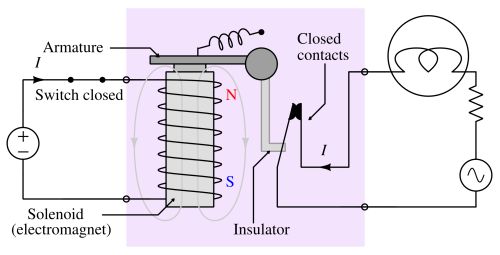
Construction of relay
A relay (electromechanical type) comprises a solenoid, yoke, and hinge, contacts (which are typically open or closed). Everything is enclosed in either a transparent or opaque casing. The solenoid and its two terminals are part of the control loop. The movable contacts form part of output loop.
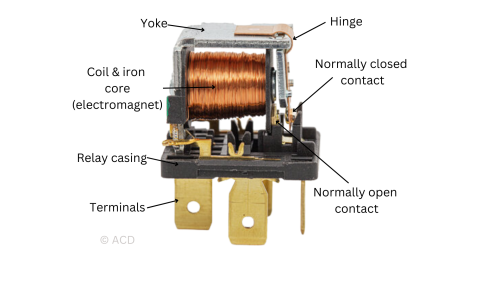
As with switches, the “normal” state of a relay’s contacts is when the coil is de-energized and not connected to any energy source. For instance, the ‘Normally Open’ (NO) contact keeps the circuit open when the relay is inactive, closing only when the relay is energized. Conversely, the ‘Normally Closed’ (NC) contact does the opposite, keeping the circuit closed when the relay is inactive and opening it when activated. The ‘Common’ (COM) contact acts as a pivot point, connecting to either the NO or NC contact depending on the relay’s state.
Open-air contacts are the best for high-current applications, but their tendency to rust and spark may cause problems in some industrial environments. Mercury and reed contacts are sparkless and won’t corrode, but they tend to be limited in current-carrying capacity.
Relay circuit schematic
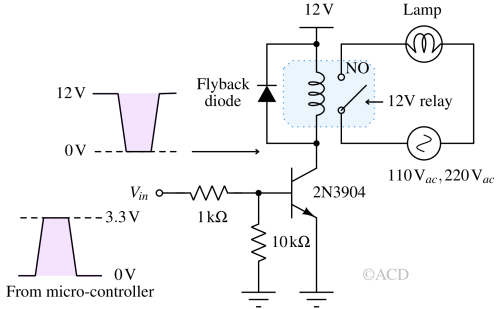
Why are Protection Devices Used in a Relay?
Relays are made using conductive coils, which are inductors. When they are energized, they carry current. Suddenly, when they are de-energized, the inductor still holds the current in the same direction. This leads to high-voltage generation at the end of the coil. If the voltage is higher than the breakdown voltage of air, arcing happens, leading to damage in the control circuit and a reduction in the lifespan of relays.
Resistors or diodes are sometimes fitted across the relay’s coil to stop or reduce voltage spikes traveling back into the control circuit and damaging sensitive components. Resistors are more durable than diodes but less efficient at eliminating voltage spikes.
How to test a relay for a fault ?
Step 1: Check in the datasheet and note the current and voltage ratings. This will prevent us from applying too much voltage or current, which can damage the relay.
Step 2: Use a Digital Multimeter (DMM) to test the relay. As we learned, a relay consists of two contact terminals: normally closed (NC) and Normally Open (NO). In a de-energized condition, check the resistance between the NO terminals. It should be infinite ohms (practically in giga ohms), and the resistance between the NC terminals should be zero.
Step 3: Use a voltage source or 9V battery with sufficient series resistance (e.g, 1kΩ) to limit the current. Apply this voltage source to the control terminal. If we can hear a click sound, the control circuit is functional. To confirm this, check the NO terminal for resistance; it should give zero resistance, while the NC terminal should give infinite resistance.
DIN 72552 Standard
DIN 72552 is a DIN standard for labeling the electric terminals in automotive wiring. The most frequently used labels for a relay are listed in the table below:
Terminal or Contact | Identification |
85 | Relay coil – Negative. |
86 | Relay coil – Positive. |
87 | Common contact |
87a | Normally Closed contact |
87b | Normally Open contact |
88 | Common contact 2 |
88a | Normally Closed contact 2 |
88b | Normally Open contact 2 |
Pole and Throw in a relay
A relay can be classified in terms of poles and throws. Poles and throws decide how many circuits can be controlled together using a relay.
What is a pole in a relay?
Pole refers to the number of circuits a switch controls. We can visualize the pole as an input. It is connected to one end of the contact. Single-pole switches manage a single electrical circuit, while double-pole switches control two separate circuits using the same control.
What is a throw in a relay?
Throw refers to the other end of the contact and indicates how many outputs the relay can switch between. If a relay can switch between only one output, it is called a single throw (ST). It is called a double throw (DT) if it can switch between two outputs.
Types of relay based on poles and throws
SPST (Single Pole Single Throw)
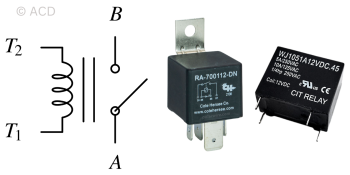
The most basic and straightforward contact type. With just one pole, these relays can control just one circuit. They are found in either one of the two configurations mentioned below :
- Normally open (NO): In a de-energized state, the contacts are open and do not conduct electricity. When energized, the contacts are closed and conduct electricity.
- Normally closed (NC): In a de-energized state, the contacts are shorted and can conduct electricity. When energized, the contacts are opened and can’t conduct electricity.
SPDT (Single Pole Double Throw)
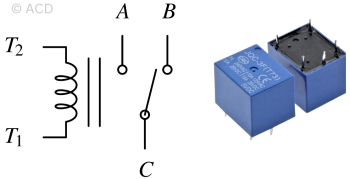
A common terminal (C) connects to either of two others (A, B), never both simultaneously. It has five terminals: two for energizing the coil (T1, T2) and three for connecting circuits (A, B, C).
DPST (Double Pole Single Throw)
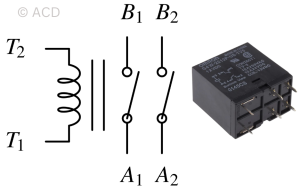
It has two common terminals, aka poles (A1 and A2). Each common terminal can connect to a single terminal, B1 and B2, respectively. The same solenoid electromagnet controls both poles. It is equivalent to two SPST relays with controls connected. It has six terminals.
DPDT (Double Pole Double Throw)
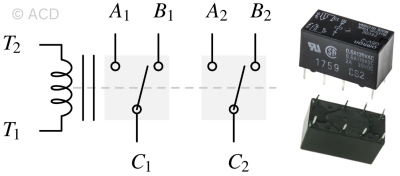
It has two common terminals (C1 and C2). Each common terminal can connect to two terminals (A1, B1) and (A2, B2). The same solenoid terminals control both. It is equivalent to two SPDT relays with controls connected. It has eight terminals in total. Two of them are for energizing the solenoid coil.
Types of Relay based on construction
Based upon construction and mechanism of control part of the relay, there are many types of relay :
Electromechanical relay
Electromechanical relay operates by mechanically moving contacts to create a contact using a solenoid. The solenoid is controlled using an external control signal.
Solid state relay
Solid state relays (SSRs) are similar to electromechanical relays in functionality but do not have moving parts. Because they do not have moving parts, the life of an SSR is much longer than that of an electromechanical relay.
Reed relay
A reed relay is a small electromagnetic switching device that integrates a coil around one or more reed switches.
Coaxial relay
Coaxial relays act like normal relays and can switch high-speed signals carried by coaxial cables. As the name suggests, they have coaxial connectors. A solenoid electromagnet is used to mechanically move the contactor.
Contactor relay
It is similar to an electromechanical relay (SPST type). Contactors are typically used in applications where high currents, typically above 15 amperes, must be switched on and off.
Other relays include force-guided contacts, Latching, Polarised, and vacuum relays.