What is a control system?
A control system is a network of devices that regulates the behavior of other systems to achieve defined outcomes. This involves control loops, processes designed to maintain a specific variable at a setpoint. Feedback mechanisms continuously monitor the system, making real-time adjustments to maintain this setpoint. Control loops are a cornerstone of control systems, ensuring precision and stability across diverse applications.
Types of control system
Primarily there are two types of control system :
- Open-loop system
- Closed-loop (Feedback) system
Open loop control system
In an open-loop system, the controller generates a control signal based solely on the input and does not consider the actual output or system response. Open-loop systems are typically used when precise control is not critical and while speed and reliability is important.
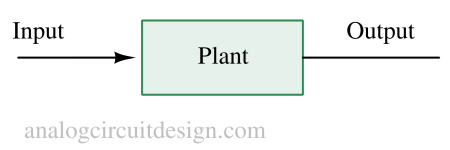
Examples of open loop control system
- Toaster: A toaster is a classic example of an open-loop control system. You set a timer, and it operates for a fixed duration regardless of the actual state of the toast. The toaster does not sense or adjust to the level of browning; it relies on a predetermined time setting.
- Lamps: Lamps illuminate whenever the light switch is in the ‘on’ position, regardless of whether the light is needed or not. We cannot set the brightness level of the lamp according to the ambient light present.
- Washing Machine: In some older or basic washing machines, you select a wash cycle (e.g., gentle, normal, heavy) and a timer, and the machine operates through the entire cycle without monitoring the cleanliness or conditions of the clothes.
- Automatic Door: Some automatic doors in public places operate on open-loop control. They open and close at predefined intervals or in response to a button press, regardless of whether someone is approaching or exiting the door.
- Traffic Signals: Traditional traffic signal systems operate based on predefined time intervals for green, yellow, and red lights. They do not adjust the timing based on traffic conditions or the presence of vehicles at the intersection.
- Irrigation System: In certain basic irrigation systems, water is turned on for a fixed duration at specific times, without considering the actual moisture levels in the soil. These systems do not adjust watering based on real-time conditions.
- Conveyor Belt: In manufacturing or material handling applications, conveyor belts may run at a constant speed, delivering products at a fixed rate, regardless of variations in product load or position.
Advantages of Open Loop Control Systems
- Simplicity: Open-loop systems are typically less complex and easier to design, implement, and maintain compared to closed-loop systems. They often involve fewer components and less intricate control algorithms.
- Low-cost: Since open-loop systems are simpler, they tend to be more cost-effective to manufacture and install. They can be easily mass-produced. This makes them a practical choice for applications where cost is a significant factor.
- Faster Response: Open-loop systems can respond rapidly to changes in input since they do not require feedback processing. This quick response can be beneficial in situations where real-time adjustments are not necessary.
- Low maintenance: Open-loop systems do not require feedback sensors to monitor the system’s output, which can reduce hardware and maintenance costs.
- Generally stable: These systems do not have a feedback control loop. So these are less prone to oscillations.
- Reliable: Since these systems consist of less number of parts, the chances are less for a failure to happen. So, these are more reliable.
Disadvantages of open loop control systems
- Inaccuracy: Open-loop systems do not incorporate feedback mechanisms to monitor the system’s actual output or performance. This means they cannot make real-time adjustments based on changes or disturbances in the system. So, these are less adaptable to changing environmental conditions.
- Sensitivity to Parameter Variations: Open-loop systems are highly sensitive to changes in system parameters. Variations in factors such as temperature, load, or component characteristics can significantly impact system performance.
- Poor Disturbance Rejection: Open-loop systems are less effective at rejecting external disturbances or variations in the system. They may not maintain stable operations when subjected to external influences.
- Steady-State Errors: Open-loop systems are prone to steady-state errors, which are deviations between the desired and actual output values that persist even in a stable system.
- Safety Concerns: In certain critical applications, the lack of feedback and error correction in open-loop systems can pose safety risks. For example, in automotive control, an open-loop system would not be suitable for tasks like antilock braking.
- Complex Tuning: Even though open-loop systems are simpler in concept, tuning them to achieve desired performance can still be challenging, especially for complex processes.
Closed loop control system
There are two types of closed-loop control systems:
- Negative feedback
- Positive feedback
Closed-loop negative feedback control systems use feedback from the system’s output to continuously adjust the control action. This feedback loop enables the system to maintain a desired state even in the presence of disturbances and uncertainties. Closed-loop control is commonly used in applications where accuracy and stability are essential. To know more in detail about the closed-loop negative feedback system, please visit this page: Fundamentals of closed-loop negative feedback systems
The positive feedback on the other hand increases the error exponentially which leads to unbounded output. To know more in detail about the closed-loop positive feedback system, please visit this page: What is a positive feedback system?
Key elements of a closed loop negative feedback control system
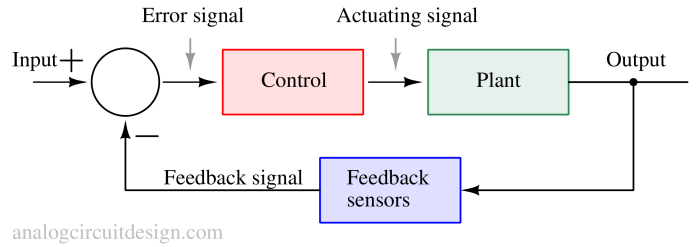
In Figure 2, we can see that a closed-loop system consists of input and output, a control mechanism, the plant (system being controlled), the output, and some feedback sensors.
Examples of closed loop negative feedback control system
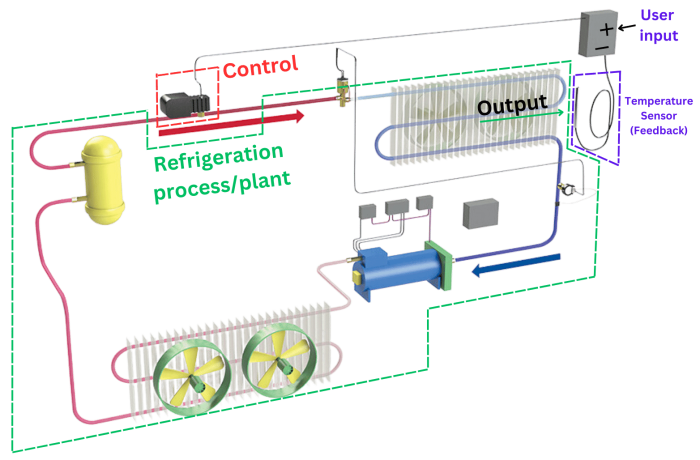
- The thermostat in HVAC and refrigeration systems: A thermostat in a heating, ventilation, and air conditioning (HVAC) system is a classic example of a closed-loop control system. It measures the room temperature and adjusts the heating or cooling system (Fig 3) to maintain the desired setpoint temperature.
- Water Level Control in Tanks: Systems that control the water level in tanks, such as those used in water treatment plants or chemical processes, use closed-loop control. Sensors monitor the water level and control valves or pumps to maintain a specific level.
- Aircraft Autopilot Systems: Aircraft autopilot systems maintain desired flight parameters (e.g., altitude, heading, and speed) by continuously adjusting control surfaces (elevators, ailerons, rudders) based on sensor feedback. These systems provide stable and precise flight.
- Speed Control in Electric Motors: Closed-loop control is used in electric motor speed control systems. Sensors measure the motor speed, and the control system adjusts the input voltage or current to maintain the desired speed.
- Robot Arm Position Control: Robot arms and manipulators use closed-loop control to accurately position the end-effector. Sensors on the joints or end-effector provide feedback to control the motors and maintain the desired position or trajectory.
- Cruise Control in Vehicles: Cruise control systems in automobiles maintain a constant speed by adjusting the throttle or brakes based on feedback from speed sensors. The driver sets a target speed, and the system works to keep the vehicle at that speed.
Advantages of closed loop (negative feedback) control system
Closed-loop feedback control systems offer several advantages compared to open-loop control systems. Here are some of the key advantages:
- Reduced Sensitivity to uncertain parameter variations: Closed-loop systems are less sensitive to variations in system parameters, making them more robust, adaptable, and reliable.
- Accuracy and Precision: They provide greater accuracy and precision with consistency in controlling the system’s output because they continually adjust the control action based on feedback information.
- Improved linearity: A nonlinear block can be made linear by using feedback. This is because the feedback system will make sure that Vout ~ kVin by adjusting the error voltage (which is very small).
- Disturbance Rejection: The feedback loop helps detect and compensate for disturbances which allow them to maintain a desired setpoint.
- Reduced Energy Consumption by optimal control: In some cases, closed-loop control can lead to energy savings as the control action is adjusted in real-time to maintain the desired output. For eg., the thermostat inside a refrigerator can turn off the compressor for a while after a particular temperature is reached.
Disadvantages of closed loop negative feedback system
- Complexity: Closed-loop systems can be more complex to design, implement, and maintain than open-loop systems, especially in multi-variable control applications. It often requires a good understanding of the system dynamics. Tuning the system is also complex.
- Cost: The sensors, controllers, and additional hardware required for feedback can add to the cost of the system. Maintenance cost is also high.
- Delay: Feedback systems can introduce time delays due to the need to sense, process, and act on information, which can affect system performance in time-critical applications.
- Potential Stability Issues: Poorly designed closed-loop systems can be susceptible to stability problems, including oscillations or instability if not tuned correctly. Also, a delay that is unaccounted for can also cause instability issues.
- Sensor and Actuator Reliability: Closed-loop systems depend on the reliability of sensors and actuators, and failures in these components can lead to system malfunctions.
- Low Bandwidth: Higher bandwidth may increase the sensitivity of the system to delay which can introduce instability of the system. So, a lower bandwidth is used so that the effect of delay is reduced.
Objectives of using a closed loop negative feedback control system
- Setpoint Tracking: The control system aims to make the system output (response) follow a desired setpoint as closely as possible.
- Regulation: The control system focuses on keeping the system output within specified bounds or at a desired operating point.
- Disturbance Rejection: Control systems are designed to minimize the effects of external disturbances on the system’s behavior.
More details about closed-loop control systems are mentioned on this page: Fundamentals of closed loop (negative feedback) system.