What is a Brushed DC motor?
Brushed DC motors represent one of the oldest, most cost-effective, and straightforward categories among DC motors. They utilize brushes for transferring current to the motor windings via mechanical commutation. The motor’s characteristics are influenced by the number of coils wound around it and the density of these coils. The armature or rotor functions as an electromagnet, while a permanent magnet serves as the field magnet. Notably, this motor operates without the need for a controller to adjust or modulate its speed.
Construction of a Brushed DC motor
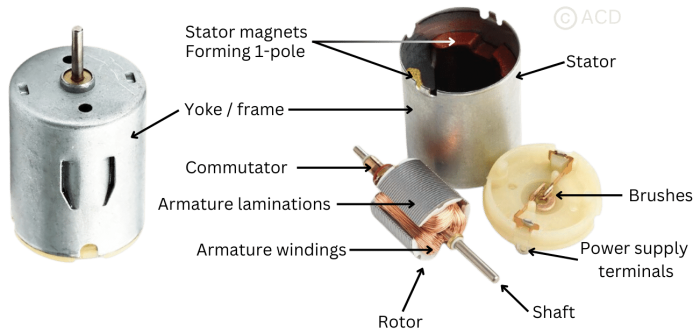
In a brushed DC motor, armature winding is on the rotor and permanent magnets are always on the stator. Utilizing metallic brushes that remain stationary to connect with the rotating commutator attached to the rotor, this setup facilitates the transfer of current to the coil. Despite their efficiency, these motors demand regular maintenance of the brushes.
Brushed DC motor working principle
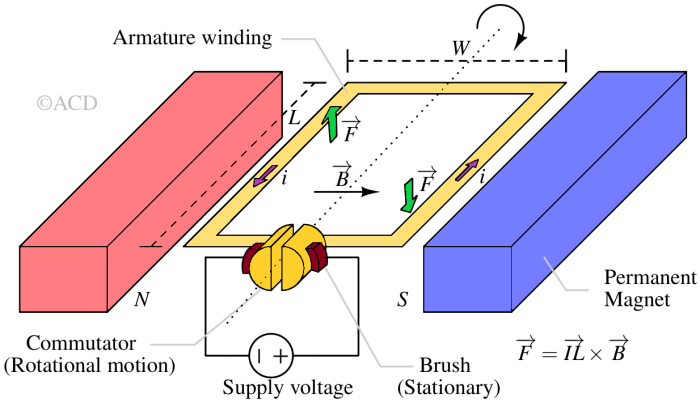
When power is sent to the motor through a DC source, electricity travels from the source to the armature through brushes placed on opposite sides of the motor shaft. These brushes are crucial as they pass electric current to the armature by touching the commutator. Once the armature receives power, it acts like a magnet. Its poles repel the poles of the permanent magnet in the stator, causing the motor’s shaft, connected to the armature, to spin with speed and torque.
The speed and strength of this rotation depend on the magnetic field around the armature. The strength of this magnetic field is generally based on the voltage at the brushes and the power of the permanent magnet in the stator.
Advantages of Brushed DC motor
- Cost-effective due to simple design.
- Can be refurbished for a longer life
- Doesn’t require a controller for steady speed. A complicated controller (ESC) is required in a brushless DC motor.
- Suitable for harsh operating conditions.
Disadvantages of a Brushed DC motor
- Less efficient due to losses in commutator and brushes.
- Produces electrical noise: The commutator’s frequent creation and disruption of inductive circuits generate considerable electrical and electromagnetic interference.
- Short lifespan and unreliability: The brushes and commutators wear out due to their constant physical contact with the shaft.
- Offers less speed than a brushless DC motor.
Applications of Brushed DC motors
While primarily utilized in household appliances and automobiles, these motors continue to serve industrial needs for various electric drives, whether low or high-powered, and operating at fixed or variable speeds. They are employed in applications such as paper machines, cranes, electric propulsion systems, sewing machines, power tools, and steel rolling mills.