What is electronic speed controller (ESC)?
The ESC, which stands for “electronic speed control”, regulates electric motor speed (throttle) and function, and is widely used in radio-controlled (RC) models (drones), particularly with brushless motors. It offers a 3-phase electric power source and can be a separate unit or integrated within the receiver, commonly seen in RC vehicles. Certain manufacturers integrate these functions on a single circuit board in RC vehicles, boats, or aircraft.
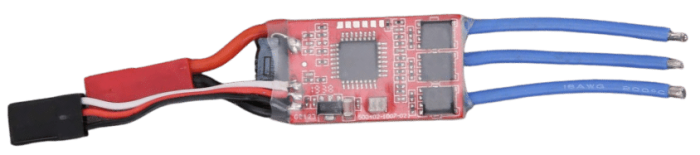
Why electronic speed control is required in BLDC motors?
A Brushed DC motor‘s speed can be changed by varying the input applied voltage. However, in the case of brushless DC motors, the input is not a constant DC voltage. The control voltage is a three-phase voltage which can be square and sinusoid wave. The frequency, amplitude, and phase/pulse-width of this input voltage can change the speed and torque of the BLDC motor. So, a separate circuit is required to control the speed of the BLDC motor.
Components of an ESC
An electronic speed controller typically comprises 4 crucial components:
- Voltage regulator or BEC (Battery Eliminator Circuit): A Battery Eliminator Circuit (BEC) functions as an electronic voltage regulator, providing power to a subsystem at a different voltage without requiring an extra battery.
- Processor: The processor in the ESC decodes receiver data, regulates motor power through FETs, and monitors motor, battery current, and voltage.
- Gate Drivers: The gate driver serves as an intermediary connecting the controller to the MOSFETs’ gates. When the microcontroller sends a low-voltage signal, the gate driver amplifies it, transmitting a high-voltage signal to the MOSFETs. MOSFETs’ gates are big and have a lot of capacitance. To charge them fast, gate drivers are vital.
- MOSFETs: Provide the current flow to throttle the electric motor in an ESC through supply. These are usually H-bridge circuits.
Working principle of Electronic speed controller (ESC)
An ESC, also known as electronic speed control, primarily uses a speed reference signal to adjust the speed of a switching network composed of field-effect transistors. By altering the switching frequency or duty cycle of the transistors, the motor speed can be effectively modified.
Diverse speed control methods are possible for BLDC (Brushless DC) motors as their speed regulation relies on adjusting the armature voltage and manipulating current pulses’ timing to different motor windings. Brushless ESC systems typically use 3-phase AC power, akin to a variable frequency drive (VFD), to operate these motors, favored for their power, efficiency, lightweight build, and durability compared to traditional brushed motors. BLDC motor controllers are notably more intricate than their brushed counterparts.
Accurate phase adjustments during motor rotation are achieved through electronic speed control. Motor rotation is commonly detected via back EMF, while some variants employ optical detectors or separate Hall Effect sensors to accommodate existing variations.
Different types of Electronic speed control (ESC)
There are different types of electronic speed controller depending on the fact if they are using sensors or not:
Sensored controller
Sensored ESCs are easy to set up and operate compared to their sensorless counterparts. Also, the startup problem is resolved in sensor-based ESCs.
However, few drawbacks. The Sensor-based ESCs tend to be pricier compared to their sensorless counterparts due to extra components and the increased complexity in their assembly. The added complexity also makes them more susceptible to issues, particularly in environments with humidity or dirt, as any disruption to the sensor’s functionality can compromise the motor’s overall control.
Sensorless systems
Sensorless systems eliminate sensors as a potential failure point, enhancing reliability. They also offer advantages such as higher maximum RPMs and compatibility with the most readily available control circuits. However, a drawback of using the motor as a sensor is the challenge of initiating a large load (e.g., traction applications) without RPM signals from the motor.
ESC controller specifications for drones
Selecting the appropriate Electronic Speed Controller (ESC) holds significant importance in the process of drone construction. It’s crucial to ensure that the ESC aligns with your aircraft’s electrical requirements without excessively draining the battery. Here are key considerations when picking an ESC.
- ESC Current Rating : Matching the ESC’s current rating to be 10 – 20% higher than the motor’s rating prevents overheating and allows leeway during maximum throttle usage. Avoid exceeding this range to keep weight in check. Testing the ESC under flight-like conditions is vital, as thermal limitations affect its performance. High temperatures and inadequate air circulation reduce the ESC’s rating and operational lifespan. Some ESCs feature two current ratings: continuous and burst. The continuous rating sustains prolonged use, while the burst rating applies only for short durations.
- ESC Voltage : ESCs have a maximum voltage limit expressed as a voltage range or cell count. For instance, an ESC rated for 3S – 8S cells supports a voltage range of 11.1 – 33.6 V. Some ESCs allow setting a switch-off voltage to alert when battery voltage drops too low (around 3.0 – 3.4 V per cell), preventing damage to the battery. These systems, known as Low Voltage Cut Off (LVC), decrease the ESC’s maximum power output and eventually shut down the motor.
- 4-in-1 ESC for Quadcopters : When wiring ESCs in a quadcopter, you can opt for one ESC per motor or use a 4-in-1 ESC featuring a single board with four motor connectors (refer to figure 10). Utilizing four ESCs helps distribute heat load, especially if motors draw high power. On the other hand, a 4-in-1 ESC proves advantageous for space-saving and reducing hardware weight.